In this second part, we will explore a few experimental and well-known techniques to replicate various distressing textures on our models. Before working on my model, I took a entire day to try various products to get accustomed to their particular application methods, drying times and effects. Most of these ideas were borrowed from the wargaming painters and army modellers who have a larger body of technical and artistic knowledge than what is generally discussed in railway modelling circles. As Martin Kovac (Night Shift on YouTube) loves to remind us, realistic modelling is all about adding texture before painting a model. This is a step I fear is too often overlooked in our corner of the hobby. Too often, we think from a technical point of view, which means we build a pristine model, paint it as it would look fresh out of the shop, then add weathering and texture in the most convoluted and inefficient way. I firmly believe, and Hunter Hughson would agree with me, that a lot of preparatory steps are mandatory before even thinking about decals. It may seems harder or more complicated, but in reality, it's much simpler and yields far superior results.
I experimented with three products, which all have their strengths and shortcomings: Vallejo Crackling Medium #70.598, Citadel Agrellan Earth crackling paint and plastic solvent. Keep in mind none of these products were formulated to crackle paint on scale models of vehicle but rather to create terrains and bases for figures in most cases. When used for their intended purpose, I can assure you their a fun to work with. But when dealing with steel vehicles with flat or riveted surfaces, a lot of experimentation is required and you can easily ruin your model. I've seen very little examples online of military guys using crackling mediums on tanks and trucks. Most of them, just like me, also consider these mediums to be amazing but extremely hard to control. Also, many art suppliers and store sell
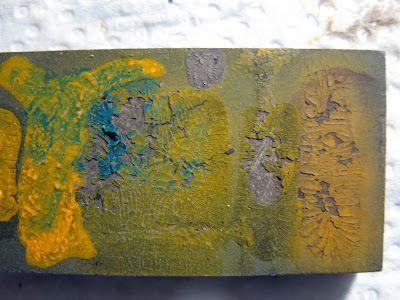 |
Thick layers create larger crackling effects and flake off |
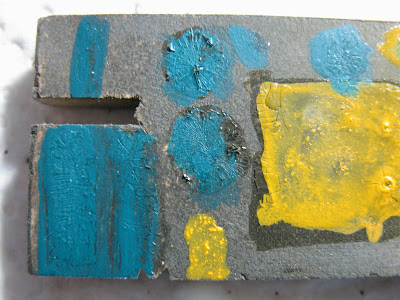 |
Thinner layers create a subtler effect |
Vallejo Crackling Medium is versatile, but it is hard to get a consistent result because it depends on thickness. Apply it in light coats and you will get a very subtle effect, even none. Apply it on thick and it will crackle and peel, sometimes to the point it can flake off. Unfortunately, even if apply thick, it's hard to predict which surface will truly crack. In the course of my experiment, I came to the conclusion thickness and drying time were crucial. In a few case, I applied a thick coat, but the perimeter dried fast and didn't really crackle while the center would flake off tremendously. I'm not saying the product is unreliable, but that working with small surfaces and trying to replicate a very specific effect takes a lot of practice.
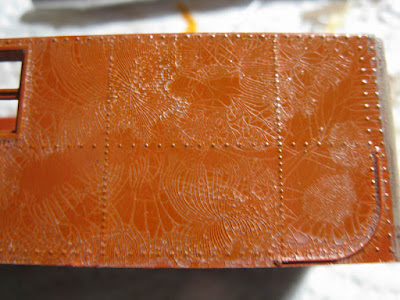 |
Vallejo Crakling Medium looks like broken glass |
Vallejo Crackling Medium can be used in two ways. The first one is to simply apply the clear product on a surface. When drying, it will crackle, leaving a transparent crackled layer that can be keep as is, of later coated with paint. Use this is you want the texture, but not the drastic effect of contrasting cracks and flakes.
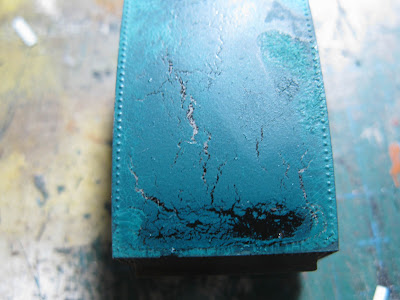 |
Acrylic paint airbrushed over wet crackling medium |
It you want contrast between colors, paint the surface the desired color (often contrasting the topcoat) and let it dry completely. Then, add a generous coat of crackling medium. Before the medium is completely dry, airbrush your top color on the wet medium and let dry. Since crackling medium is made of two components that don't dry at the same speed (hence the crackling), it will provide also crackle the top coat. The effect can be extremely convincing and beautiful! However, airbrushing paint over a viscous liquid isn't extremely practical, particularly when dealing with intricate small scale models. I believe this multiple layer technique as a lot of potential, but it requires more experimentation.
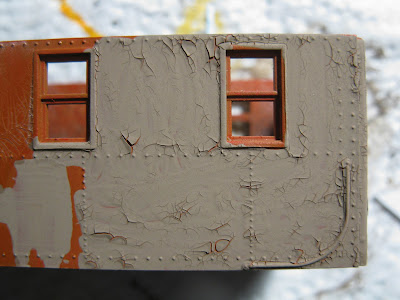 |
Egrellan Earth makes beautiful chipping effects, but it's hard to control |
The second product used was Citadel Egrellan Earth crackling paint sold by Games Workshop. This texture paint is well known within wargaming enthusiasts to create crackled desert soil on figure bases. As such, most people apply it sloppily and thickly on bases and leave it to dry. If applied thin, it will create multiple small cracks like Vallejo Crackling Medium. If applied thick, cracks are large and paint starts to flake off, creating a very convincing result. However, when dealing with a railway car, this sloppiness that is desirable on a base is no longer welcome.
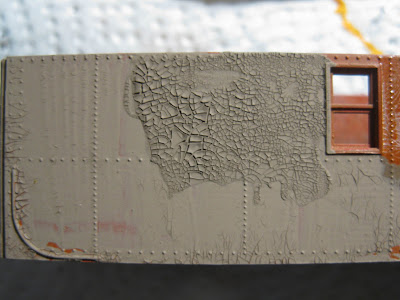 |
A troweled thick layer gives the best results |
To control thickness, I found out it was better to trowel the paint over the shell with a bit of styrene or cardboard. That way, you ensure the crackling effect will be regular and systematic on all the surface. If applied with a brush, it is likely to create zone with many cracks and others almost pristine. This can be used to our advantage because flaking will occur around details, window frames, structural members, etc., where flaking do happen in real life.
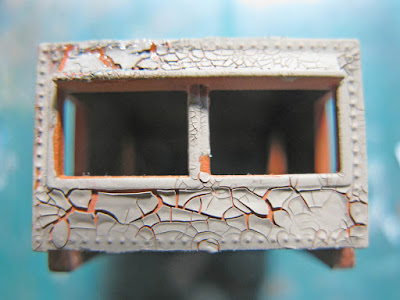 |
A very thick coat on small details produces drastic effects |
Another advantage with Egrellan Earth is that it's so thick you can apply it precisely with a fine brush on certain details and it will crack exactly where you want it. Unfortunately, like Vallejo Crackling Medium, it is really hard to predict were crackling will happen and how. You need a lot of practice on various surfaces to get a hang of this technique. That said, you can always come back later and pick up some specific area where you add another layer. However, be advised this paint is extremely thick and will obscure some details. It could be a problem, but I found out on prototype pictures that where paint flakes, you generally loose completely the details because chipping obscure them.
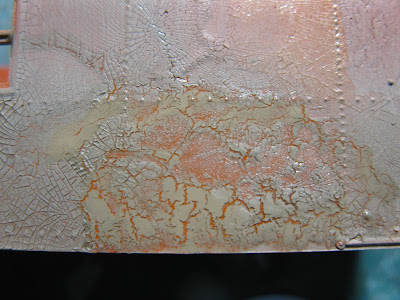 |
Egrellan Earth over dried Vallejo Crackling Medium |
A strange thing I discovered is you can apply Egrellan Earth over Vallejo Crackling Medium and it will produce an interesting crackling effect. It can be done days after Vallejo product is applied and the chemical reaction will still occur. But there is a big caveat: you must apply Egrellan Earth in one single pass with a brush or an airbrush because it will reactivate the Crackling Medium in a matter of a few seconds. If you continue to brush over the area, a thick gunk will start to form which, at this point, will completely ruin the surface.
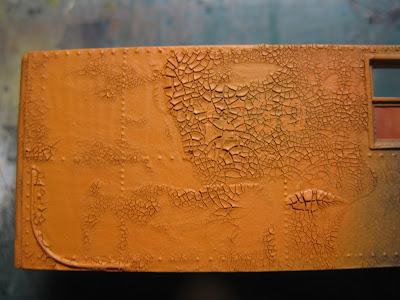 |
Egrellan Earth must be painted if you want another colot |
Unfortunately, there is a big problem with Citadel crackle paint; it comes only in two colors. Egrellan Earth is a clay color ideal for soil while Martian Ironearth is a reddish hue perfect for... Martian dioramas! It means if you want another color, you'll have to paint the surface when everything is dry, which means you will probably covered up the cracks, taking away a big part of the effect. In this regard, I found out it was advisable to airbrush the color at low pressure from an angle. That way, very little paint gets into the cracks. Also, apply thin coats, building up your color. You really don't want a wet coat that will run all over the cracks. 24 hours later, make a dark oil paint wash and apply it on the surface. The dark pigment will make the cracks pop out once again. You can use odorless solvent to clean the flakes surface for all pigment, which will stay into the recesses.
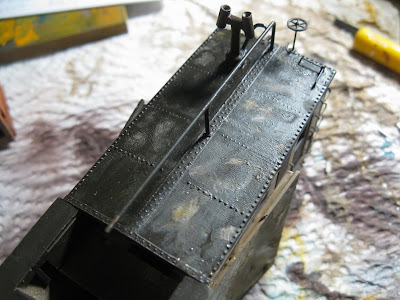 |
Plastic roof textured with solvent cement dabbed with a stiff brush |
The last product is not exactly a crackling product, but rather a chemical reaction occurring when plastic solvent start to melt surfaces. Military modellers use this trick to add a cast iron texture to large plain surfaces. It's easy, use a stiff brush and soak it in solvent. Then dab the model surface with your brush until is starts melting. The brush hairs will imprint a finely granulated texture on the plastic which, if done correctly, will replicated a slightly imperfect cast steel surface. This is particularly useful for many cast parts on models, including truck sideframes (when they aren't made of Delrin). It can also be used to replicate car roof covered with roofing cement and other similar textured products.
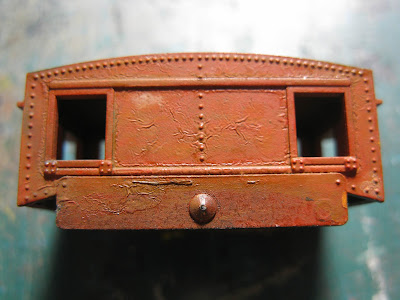 |
Paint distressed with several light coats of solvent cement |
Another option with solvent cement is simply to soak small surfaces that are already painted or primed. After about 3 seconds, most paints will start to wrinkle, creating a pattern that can be controlled as you wish. Simply accelarate the evaporation time and you can decide when the reaction stops. Unfortunately, this trick doesn't work the same with all paints and can be hard to predict. But once you know how the paint react, you can easily texture and entire model or simply some specific areas. Since it's not a paint, you don't add layer and it is possible to come back and touch up some areas to build up the effect.
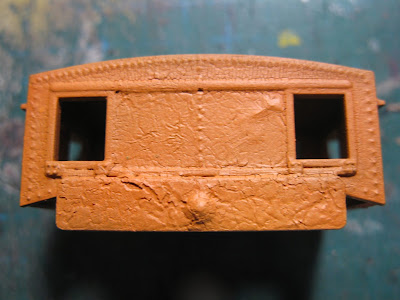 |
Solvent wrinkles painted over with acrylics look great |
As a side note, Chris Mears asked me if crackling medium could be used to replicate worn out asphalt roads and I believe it could. I think a coat of Vallejo Crackling medium on a road surface would create an interesting and subtle pattern that could then be painted and covered with a dark wash to make cracks pop out. It is certainly an idea I wouldn't mind trying on the Donohue access road in Clermont.